Präzision + breites Produktspektrum | Form- und Maßtoleranzen für höchste Anforderungen
Präzision + breites Produktspektrum | Form- und Maßtoleranzen für höchste Anforderungen
CNC Drehen und Fräsen - Zerspanende Herstellung
Die spanende Herstellung von Sonderschrauben und Muttern mit Dreh- und Fräsmaschinen stellt verglichen mit den Umformverfahren nur einen Randbereich bei der Produktion von Verbindungselementen dar. Trotzdem hat dieses Fertigungsverfahren seine Existenzberechtigung.
So können vor allem kleine Stückzahlen an Zeichnungsteilen und Sonderteilen ohne die Erstellung von teuren Umformwerkzeugen erstellt werden. Dieser Vorteil weitet sich vor allem dann aus, wenn die Verbindungselemente aus auf den Einsatzfall ausgelegten speziellen Werkstoffen hergestellt werden müssen. Weiter ist das Verfahren sinnvoll, wenn spezielle Maße oder Toleranzen (abweichend von Normen) bei Sonderteilen wie Sonderschrauben eingehalten werden müssen.
Häufig wird speziell bei der Herstellung von Sonderschrauben oder Bolzen eine Kombination aus zerspanenden und umformenden Verfahren zum Einsatz gebracht. So werden zum Beispiel die Schraubenrohlinge (ohne Gewinde) zerspanend hergestellt und anschließend das Gewinde in einem Kaltumformverfahren eingebracht.
CNC-Drehen
Das CNC-Drehen ist ein Fertigungsverfahren zur Herstellung von Drehteilen, insbesondere Präzisionsdrehteilen, mithilfe einer CNC-gesteuerten Drehmaschine. Diese Methode ermöglicht es, komplexe Formen und enge Toleranzen zu erreichen.
Beim CNC-Drehen wird ein roher Werkstoff in eine rotierende Spindel eingespannt. Das Werkstück wird dann mit verschiedenen Werkzeugen bearbeitet, um die gewünschte Form und Oberfläche zu erhalten. Die CNC-Steuerung ermöglicht es, die genauen Bewegungen und Bearbeitungsschritte des Werkzeugs präzise zu steuern.
Durch CNC-Drehen können verschiedene Arten von Drehteilen hergestellt werden, wie beispielsweise Achsen, Buchsen, Sonderschrauben, Bolzen und viele andere Komponenten. Die Verwendung von CNC-gesteuerten Drehmaschinen ermöglicht eine hohe Wiederholgenauigkeit und Präzision, was besonders wichtig ist, wenn es um die Herstellung von Präzisionsdrehteilen geht.
Die Vorteile des CNC-Drehens liegen in der effizienten Produktion von Drehteilen in großen Stückzahlen, der Möglichkeit, komplexe Formen und Geometrien herzustellen, sowie der hohen Genauigkeit und Wiederholbarkeit. CNC-Drehen findet Anwendung in verschiedenen Industriezweigen, wie der Automobilindustrie, Luft- und Raumfahrt, Medizintechnik, Elektronik und vielen anderen Bereichen, wo Präzisionsdrehteile benötigt werden.
Beim CNC-Drehen unterscheidet man grundsätzlich zwischen Innen- und Außendrehen, wobei beide Arten von einer CNC-Drehmaschine ausgeführt werden können. Unterteilt wird das Drehverfahren anhand der Vorschubrichtung in Quer- und Längsdrehen. Abhängig von der zu bearbeitenden Oberfläche gibt es noch weitere Unterteilungen beim Drehen.
Gängige Verfahrenstechniken sind beispielsweise:
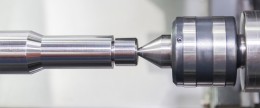
Formdrehen wird häufig in der Herstellung von Präzisionsdrehteilen eingesetzt, bei denen komplexe Formen und enge Toleranzen gefordert sind. Es ermöglicht die effiziente Produktion von Teilen mit hoher Genauigkeit und Oberflächengüte.
Beim Formdrehen werden spezielle Werkzeuge und Werkzeughalter verwendet, um die gewünschte Form des Werkstücks zu erzeugen.
Im Gegensatz zum konventionellen Drehen, bei dem das Werkstück hauptsächlich zylindrisch geformt wird, ermöglicht das Formdrehen die Herstellung von komplexen Konturen, wie beispielsweise Nuten, Radien, Flächen oder auch Gewinde. Dies wird durch den Einsatz von speziellen Werkzeugen mit unterschiedlichen Geometrien und Schneidkanten erreicht.
Die CNC-Steuerung ermöglicht es, die Bewegungen des Werkzeugs präzise zu steuern und die gewünschten Formen in das Werkstück zu drehen. Dabei können verschiedene Parameter, wie z.B. die Schnittgeschwindigkeit, der Vorschub und die Zustellung, angepasst werden, um optimale Ergebnisse zu erzielen.
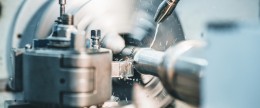
Das Plandrehen wird oft verwendet, um Flächen zu bearbeiten, wie beispielsweise Stirnseiten, Planflächen, Absätze oder auch um Kanten zu entgraten. Es kann auch verwendet werden, um bestimmte Konturen oder Formen zu erzeugen, indem das Werkzeug entsprechend programmiert wird.
Beim Plandrehen handelt es sich um eine grundlegende Technik des CNC-Drehens, bei der das Werkzeug quer zur Drehachse des Werkstücks bewegt wird. Dadurch wird die Außenseite des Werkstücks bearbeitet, um eine ebene Fläche zu erzeugen oder eine bestimmte Kontur zu formen.
Beim Plandrehen wird das Werkstück in der Spannzange oder auf dem Futter der CNC-Drehmaschine eingespannt. Das Werkzeug bewegt sich dann entlang einer geraden Linie, die senkrecht zur Drehachse des Werkstücks verläuft. Diese Bewegung ermöglicht es, Material von der Oberfläche des Werkstücks abzutragen und eine ebene Fläche zu erzeugen.
Die Vorteile des Plandrehens liegen in der einfachen Handhabung, der effizienten Materialabtragung und der Möglichkeit, präzise Flächen und Konturen zu erzeugen. Es wird in verschiedenen Branchen eingesetzt, wie beispielsweise in der Automobilindustrie, im Maschinenbau, in der Metallverarbeitung und in vielen anderen Bereichen, in denen eine präzise Bearbeitung von Flächen erforderlich ist.
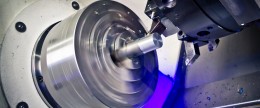
Im Vergleich zum konventionellen Drehen ermöglicht das Wälzdrehen eine höhere Produktivität und Oberflächengüte. Es ist besonders für die Herstellung von Drehteilen mit rotationssymmetrischer Form wie Wellen, Bolzen, Achsen und Rohren geeignet.
Beim Wälzdrehen wird das Werkzeug entlang der Drehachse des Werkstücks bewegt, während das Werkstück selbst eine rotierende Bewegung ausführt. Das Werkzeug drückt dabei gegen das Werkstück und erzeugt so die gewünschte Form.
Beim Wälzdrehen wird eine spezielle Wälzdrehmaschine oder eine CNC-Drehmaschine verwendet, die über eine entsprechende Steuerung verfügt. Die Steuerung ermöglicht die präzise Bewegung des Werkzeugs entlang der Drehachse und die Steuerung der Schnittgeschwindigkeit, des Vorschubs und der Zustellung.
Das Wälzdrehen bietet mehrere Vorteile, darunter eine höhere Produktivität, eine verbesserte Oberflächengüte, eine längere Werkzeugstandzeit und eine erhöhte Maßgenauigkeit. Es wird in verschiedenen Branchen eingesetzt, wie beispielsweise in der Automobilindustrie, im Maschinenbau und in der Luft- und Raumfahrtindustrie.
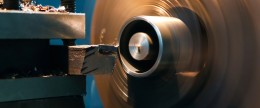
Beim Runddrehen handelt es sich um eine grundlegende Technik, bei der das Werkstück auf einer CNC-Drehmaschine bearbeitet wird, um Drehteile mit zylindrischen Formen herzustellen.
Beim Runddrehen wird das Werkstück in der Spannzange oder im Futter der CNC-Drehmaschine fixiert. Das Werkzeug bewegt sich dann entlang der Rotationsachse des Werkstücks, um Material abzutragen und die gewünschte zylindrische Form zu formen. Diese Methode wird genutzt, um zylindrische Teile wie Wellen, Bolzen, Achsen und andere zu produzieren.
Runddrehen ermöglicht eine präzise Bearbeitung von Werkstücken mit hoher Oberflächengüte. Die CNC-Steuerung erlaubt eine genaue Kontrolle der Werkzeugbewegungen und eine präzise Bearbeitung. Darüber hinaus können verschiedene Werkzeuge und Schneidwerkzeuge eingesetzt werden, um unterschiedliche Konturen, Gewinde oder andere Merkmale zu formen.
Runddrehen findet Anwendung in zahlreichen Industrien, einschließlich der Automobilindustrie, dem Maschinenbau, der Luft- und Raumfahrtindustrie und vielen anderen, in denen zylindrische Teile benötigt werden.
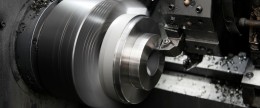
Profildrehen nutzt spezielle Werkzeuge mit verschiedenen Schneidkanten und Profilen, um gewünschte Formen und Konturen zu formen. Diese Werkzeuge können in der CNC-Drehmaschine eingesetzt werden und erlauben die Bearbeitung komplexer Formen wie Nuten, Radien, Kanten, Gewinde und andere Konturen.
Beim Profildrehen wird das Werkzeug entlang der Drehachse des Werkstücks bewegt, um die gewünschten Konturen zu erzeugen.
Die CNC-Steuerung ermöglicht es, die Bewegungen des Werkzeugs präzise zu steuern und die gewünschten Konturen in das Werkstück zu drehen. Die Parameter wie Schnittgeschwindigkeit, Vorschubrate und Zustellung können angepasst werden, um optimale Ergebnisse zu erzielen.
Das Profildrehen wird häufig in der Herstellung von komplexen Drehteilen eingesetzt, bei denen spezifische Konturen und Formen erforderlich sind. Es findet Anwendung in verschiedenen Branchen wie Automobilindustrie, Luft- und Raumfahrt, Maschinenbau, Medizintechnik und vielen anderen.
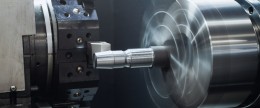
Dieses Fertigungsverfahren wird häufig eingesetzt, um Gewinde auf Schrauben, Bolzen und anderen Bauteilen herzustellen.
Schraubdrehen im Bereich CNC-Drehen bezieht sich auf das Herstellen von Gewinden auf einem Werkstück mithilfe einer CNC-Drehmaschine.
Beim Schraubdrehen wird ein Schneidwerkzeug verwendet, um spiralförmige Rillen in das Werkstück zu schneiden, um ein Gewinde zu erzeugen.
Durch die Verwendung einer CNC-Drehmaschine können komplexe Gewindegeometrien mit hoher Präzision hergestellt werden.
Mehrspindeldrehen für mittlere bis große Serienproduktion von Präzisionsdrehteilen
Mehrspindeldrehen bzw. Multispindeldrehen ist ein Verfahren im Bereich der CNC-Drehbearbeitung, bei dem mehrere Spindeln gleichzeitig verwendet werden, um mehrere Bearbeitungsvorgänge auf einem Werkstück durchzuführen. Im Gegensatz zum herkömmlichen Einzelspindeldrehen, bei dem nur eine Spindel zum Drehen des Werkstücks verwendet wird, ermöglicht das Multispindeldrehen das gleichzeitige Bearbeiten mehrerer Werkstücke.
Es können verschiedene Bearbeitungsvorgänge wie Drehen, Bohren, Gewindeschneiden oder Fräsen gleichzeitig durchgeführt werden. Dadurch können mehrere Werkstücke in einem Durchgang bearbeitet werden, was zu einer erheblichen Steigerung der Produktivität führt.
Das CNC Mehrspindeldrehen wird häufig in der Serienproduktion eingesetzt, bei der große Stückzahlen hergestellt werden müssen. Es ermöglicht eine effiziente und kostengünstige Bearbeitung von Werkstücken, da mehrere Bearbeitungsschritte in einem Durchgang durchgeführt werden können.
Vorteile des Mehrspindeldrehens
- Erhöhte Produktivität – Durch die Verwendung mehrerer Spindeln können mehrere Bearbeitungsvorgänge gleichzeitig durchgeführt werden. Dadurch wird die Bearbeitungszeit pro Drehteil erheblich reduziert, was zu einer höheren Produktivität führt.
- Kosteneinsparungen – Durch die gleichzeitige Bearbeitung mehrerer Drehteile in einem Durchgang können Kosten für Maschinenlaufzeiten, Werkzeugwechsel und Rüstzeiten gespart werden. Dies führt zu niedrigeren Produktionskosten pro Drehteil.
- Hohe Präzision – Das Multispindeldrehen ermöglicht eine präzise Bearbeitung der Drehteile, da die verschiedenen Bearbeitungsschritte in einem einzigen Prozess ablaufen. Dadurch werden mögliche Fehler oder Ungenauigkeiten minimiert.
- Flexibilität – Mehrspindeldrehmaschinen bieten die Möglichkeit, verschiedene Bearbeitungsschritte und Werkzeuge zu kombinieren. Dadurch können komplexe Drehteile mit unterschiedlichen Bearbeitungen in einem Durchgang hergestellt werden.
Präzisionsdrehteile für mittlere bis große Serienfertigung
Wenn Sie eingebettete Videos auf www.gueldner.com anzeigen und abspielen, ist es möglich, dass der Anbieter (YouTube) Ihre Zugriffe speichern und Ihr Verhalten analysieren kann. Wenn Sie die Inhalte aktivieren, also dem Anzeigen und Abspielen zustimmen, wird ein Cookie auf Ihrem Computer gesetzt, um festzuhalten, dass Sie in Ihrem Browser zugestimmt haben. Dieses Cookie speichert keine personenbezogenen Daten.
Weitere Informationen finden Sie in unserer Datenschutzerklärung und auf der Cookie-Seite.
Alternativ können Sie auch diesen Link verwenden, um das Video direkt auf der Plattform des Anbieters aufzurufen: https://youtu.be/EwyBzrFChC8
CNC-Fräsen
CNC-Fräsen ist ein Verfahren zur präzisen Bearbeitung von Werkstücken aus Metall zur Herstellung von Frästeilen. Bei CNC-Fräsen wird ein computergesteuertes Fräswerkzeug eingesetzt, welches das Werkstück schrittweise abträgt, um die gewünschte Form zu erzeugen.
Der Einsatz von CNC-Fräsen bietet zahlreiche Vorteile bei der Herstellung von Frästeilen. Zum einen ermöglicht die computergesteuerte Steuerung eine hohe Präzision und Wiederholgenauigkeit, was zu exakten Ergebnissen führt. Darüber hinaus können Präzisionsfrästeile mit komplexen Formen und mit einer großen Genauigkeit hergestellt werden.
Ein weiterer Vorteil des CNC-Fräsens ist die Effizienz. Da das Verfahren automatisiert ist, können große Mengen an Werkstücken in kurzer Zeit bearbeitet werden. Dies führt zu einer erhöhten Produktionsgeschwindigkeit und einer Reduzierung der Kosten.
CNC-Fräsen findet Anwendung bei der Herstellung von Prototypen, Einzelteilen, Kleinserien und auch bei der Massenproduktion für verschiedenste Branchen wie den Maschinenbau, Automotive sowie Medizintechnik.
Zusätzlich gibt es abhängig von der Geometrie des Werkzeugs unterschiedliche Arten des CNC-Fräsens. Einige der bedeutendsten Herstellungsprozesse sind zum Beispiel:
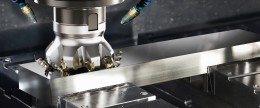
Planfräsen wird bevorzugt bei präzisen ebenen Oberflächen eingesetzt. Das Finish bringt Frästeile zum Glänzen!
CNC-Planfräsen ist ein Verfahren, bei dem das Fräswerkzeug in einer senkrechten Position zum Werkstück platziert wird. Üblicherweise wird das Werkzeug mit der Oberseite nach unten auf das Werkstück gelegt. Sobald es eingerastet ist, schleift die Fräserspitze die Oberfläche des Werkstücks ab und entfernt dabei einen Teil des Materials.
Es gibt verschiedene Arten von Planfräsbearbeitungen für Präzisionsfrästeile, einschließlich Standard-Planfräsen und Schwerlast-Planfräsen.

Wälzfräsen, ein Unterbereich des Fräsens, ist ein Herstellungsprozess, der für die Vor- und Endbearbeitung von Zahnradverzahnungen eingesetzt wird.
Wälzfräsen gehört zu den kontinuierlichen Verzahnungsverfahren und zeichnet sich durch seine Flexibilität und hohe Produktivität aus. Die Drehbewegung des Fräsers erzeugt die eigentliche Schneidbewegung. Mit Wälzfräsen können alle Zähnezahlen, Profilverschiebungen und Schrägungswinkel erzeugt werden.
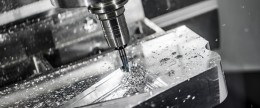
Schraubfräsen wird zur Erzeugung von schraubenförmigen Strukturen eingesetzt. Dazu gehören insbesondere Gewinde, Spindeln und Zylinderschnecken.
Beim Schraubfräsen von Langgewinden wird ein einprofiliger Gewindefräser verwendet. Hierbei entspricht der Vorschub der Gewindesteigung. Die Werkzeugachse ist leicht zur Gewindeachse geneigt, was an das Gewindedrehen erinnert.
Für das Schraubfräsen von Kurzgewinden wird ein mehrprofiliges Werkzeug eingesetzt, das parallel zum Gewinde ausgerichtet ist. Auch in diesem Fall entspricht der Vorschub der Gewindesteigung. Es ist jedoch nur etwas mehr als eine volle Umdrehung des Werkstücks notwendig, um das Gewinde zu erzeugen. Dieser Vorgang ähnelt dem Gewindestrehlen.
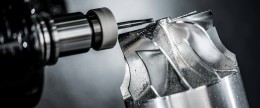
Mit dem Profilfräsen können Frästeile erzeugt werden, die Formelemente wie Radien und Schrägen aufweisen.
Profilfräsen nutzt Profilfräser, die das Negativ der zu erzeugenden Form enthalten, um unterschiedliche Profile wie T-Nuten, Schwalbenschwanznuten oder Span-Nuten auf großen Fräsern zu erstellen. Bei rotierenden Werkstücken können zudem umlaufende Nuten gefertigt werden. Je nach Art der Vorschubbewegung können runde, gerade oder beliebige Formen hergestellt werden. Da viele Formelemente an Werkstücken, wie Radien und Schrägen, genormt sind, gibt es auch entsprechend genormte Profilfräser.
Es werden drei Arten von Profilfräsen unterschieden: Längs-Profilfräsen erfolgt mit einer geradlinigen Vorschubbewegung, Rund-Profilfräsen mit einer kreisförmigen Vorschubbewegung und Form-Profilfräsen mit einer beliebigen Vorschubbewegung.
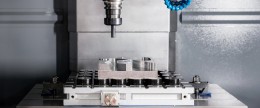
Das Formfräsen ist besonders für dreidimensionale Frästeile geeignet.
Formfräsen nutzt Werkzeuge, die nicht die Form enthalten, die erzeugt werden soll. Durch Steuerung der Vorschubbewegung können vielfältige dreidimensionale Formen erstellt werden.
Neben dem Freiformfräsen gibt es auch das Nachformfräsen auch unter Kopierfräsen bekannt. Diese Fräsverfahren sind seit der Einführung der CNC-Steuerung weniger gebräuchlich.
Kinematisches Formfräsen verwendet Getriebe, wie Kurvenscheiben oder Trommelkurven, zur Bewegungserzeugung. Diese Methode wurde früher zur Herstellung großer Serien identischer Werkstücke verwendet, ist heute jedoch selten.
NC-Formfräsen nutzt eine numerische Steuerung, oft in Form einer CNC-Steuerung. Damit können neben den drei Bewegungen in jeder Achsenrichtung auch die Werkzeuge um zwei Achsen geschwenkt werden, um komplexe Formen zu erzeugen. Dieses Verfahren wird zur Herstellung von Gesenken im Formenbau, zur Herstellung von Gussformen oder für Turbinenschaufeln verwendet.
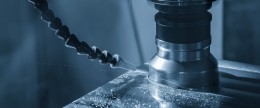
Tauchfräsen ermöglicht das Herstellung von Frästeilen mit komplexen Formen und Konturen, da das Werkzeug in verschiedenen Winkeln und Tiefen eintauchen kann.
Beim Tauchfräsen handelt es sich um ein Verfahren der Fräsbearbeitung, bei dem das Fräswerkzeug direkt in das Werkstück eintaucht, um Material abzutragen. Im Gegensatz zum Planfräsen, bei dem das Werkstück bereits vor dem Fräsvorgang positioniert ist, erfolgt beim Tauchfräsen der Eintauchvorgang des Werkzeugs in das Werkstück.
Das Tauchfräsen wird häufig bei der Bearbeitung von tiefen Taschen oder Hohlräumen verwendet, bei denen das Werkzeug nicht von der Seite in das Material eindringen kann.
Die Vorteile des Tauchfräsens liegen unter anderem in der Möglichkeit, tiefe Löcher oder Taschen zu bearbeiten, der Präzision bei der Formgebung und der Effizienz bei der Materialabtragung. Allerdings erfordert das Tauchfräsen aufgrund des Eintauchvorgangs eine sorgfältige Programmierung und Werkzeugauswahl, um eine sichere und präzise Bearbeitung zu gewährleisten.
Sonderschrauben Güldner GmbH & Co. KG erhebt und verarbeitet die in dem Formular angegebenen personenbezogenen Daten, um für Sie die gewünschte Anfrage zu bearbeiten. Bitte beachten Sie bei den Formularen die Markierung der Pflichtfelder. Rechtsgrundlage für diese Verarbeitung, der zwingend erforderlichen Daten, ist Art. 6 Abs. 1 lit. b DSGVO, Durchführung einer vorvertraglichen Maßnahme. Die Verarbeitung der von Ihnen freiwillig mitgeteilten Daten erfolgt auf der Grundlage von Art. 6 Abs. 1 lit. f DSGVO. Danach ist eine Verarbeitung zulässig, die zur Wahrung der unserer berechtigten Interessen erforderlich ist. Unser berechtigtes Interesse besteht darin, mit Ihnen, unseren Kunden, Kontakt zu haben, unsere Beratungsqualität zu verbessern und Sie bei möglichen Rückfragen einfacher kontaktieren zu können. Die erhobenen Daten werden von uns nur solange gespeichert, wie es für die Bearbeitung Ihrer Anfrage sowie zur Kontaktaufnahme mit Ihnen erforderlich ist. Danach werden sie gelöscht.
Ergänzende Datenschutzhinweise, insbesondere zu Ihren Rechten auf Auskunft, Berichtigung, Löschung, Einschränkung der Verarbeitung, Widerspruch und Beschwerde, finden Sie in unserer Datenschutzerklärung.