Coating
Types of coating for screws and fasteners
When it comes to joining metal parts, screws play a crucial role. However, to ensure that these connections remain durable and reliable, it is important to protect the screws and other fasteners from corrosion and wear. This is where coatings come into play. Below you can see the most common screw coatings and coating types for fasteners that we offer.
Galvanic coating of special screws and fasteners
Electroplating offers optimum corrosion protection and improved durability for screws and fasteners. Find out more about it here.
Galvanic coatingThis coating is particularly resistant to chemical and mechanical influences.
Frequently used on components subject to high stress, such as screws and steel components, the zinc flake coating extends the service life and performance of the parts. The process is usually carried out by dip-spinning or spraying, followed by heat setting, which forms an even protective layer.
The zinc flake coating significantly increases the corrosion resistance of the metal, which protects the components from environmental influences and mechanical stresses.
Nickel plating a metal is a method in which a thin layer of nickel is applied to the surface of the metal. This process is often carried out for aesthetic reasons, to protect the metal from corrosion or to improve its hardness and wear resistance.
There are various methods that can be used for nickel plating. Electrolytic nickel plating is a common method. In this process, the metal to be used for nickel plating is immersed in an electrolyte bath as the cathode. As the anode, nickel ions are dissolved from the anode by the electric current flow and deposited on the surface of the metal. This results in an even layer of nickel on the metal.
Electroless nickel plating is another approach. Here, the metal is immersed in a mixture of nickel compounds. Nickel is transferred from the solution to the surface of the metal through chemical reactions. This method of nickel plating is particularly suitable for parts with complex shapes.
Nickel plating has numerous advantages. Firstly, the metal is protected from corrosion by the nickel coating. Nickel, an extremely resistant metal, protects the surface of the metal from moisture, acids and other harmful substances. In addition, nickel plating increases the wear resistance and hardness of the metal. Nickel is a hard metal that forms a strong layer on the surface. This makes the metal more resistant to scratches, abrasion and other mechanical stresses.
Nickel plating is also possible for aesthetic reasons. Nickel plating gives metals a shiny and silvery look that enhances the appearance. It is often used on jewelry, fittings, vehicle components and other items where an attractive appearance is important.
In summary, nickel plating is a technique used to protect metal from corrosion, improve hardness, wear resistance and appearance. Different processes can be used depending on the specific requirements and properties of the metal. Nickel plating is an established technique that is used in many industries.
Veralizing is often used for components that are exposed to high loads, such as tools, machine parts or wear parts. The thick nickel coating makes the surface of the metal more resistant to abrasion, scratches and other mechanical influences. This improves the service life and performance of the components.
As a rule, nickel plating is carried out by electrolytic nickel plating. The metal is immersed in an electrolyte bath as the cathode, while nickel serves as the anode. Nickel ions are released from the anode by the electric current flow and deposited on the surface of the metal. In order to achieve a thick and uniform nickel coating, this process is carried out over a longer period of time.
Alkalization increases the hardness and wear resistance of the metal. The thick nickel coating makes the surface more resistant to mechanical stress, which extends the service life of the components. As nickel is a resistant metal and forms a protective layer on the surface, the aluminizing process also protects against corrosion.
Metal chrome plating is a process in which a thin layer of chrome is applied to the surface of a metal. This process is often used for aesthetic reasons or to protect the metal from corrosion and increase its hardness.
There are various methods that can be used for chrome plating. One frequently used method is electrolytic chrome plating. In this process, the metal to be chrome-plated is immersed in an electrolyte bath as the cathode. The chromium is used as an anode and chromium ions are dissolved from the anode and deposited on the surface of the metal by the flow of electric current. This forms an even layer of chromium on the metal.
A different method is chemical chromium plating. In this process, the metal is immersed in a solution containing chromium compounds. Chemical reactions deposit the chromium from the solution onto the surface of the metal. This method is often used when the metal has a complex shape or when a uniform layer thickness is required.
Chrome plating offers various advantages. Firstly, the chrome coating protects the metal from corrosion. Chrome forms a protective layer on the surface that protects the underlying metal from moisture, acids and other harmful influences.
Furthermore, chrome plating increases the hardness and wear resistance of the metal. Chrome is a hard metal and forms a resistant layer on the surface. This makes the metal more resistant to scratches, abrasion and other mechanical stresses.
Chrome plating also offers aesthetic benefits. Chrome coatings often have a shiny and reflective look that enhances the appearance of the metal. This is often applied to vehicle parts, fittings, household appliances and other products where an attractive appearance is important.
- Bright chrome-plated: high gloss
- Matt chrome-plated: matt sheen (satin sheen)
Drum chrome plating is not possible.
The coating of a metal surface with a thin layer of brass is known as brass plating. The brass alloy consists mainly of copper and zinc. Brass plating is often used to protect the metal from corrosion, to create a decorative surface or to improve electrical conductivity.
There are a variety of techniques to be successful in brass plating. Electrolytic brass plating is a widely used technique. In this process, the metal to be used for gauging is immersed in an electrolyte bath as a cathode. A brass anode is also immersed in the bath. Copper and zinc ions are dissolved from the anode by the electric current flow and deposited on the surface of the metal. This creates an even layer of brass on the metal.
Chemical brassing is a further method. The metal is immersed in a solution containing copper and zinc compounds. Copper and zinc ions are deposited from the solution onto the surface of the metal through chemical reactions. This process is often used when the screws or parts have complex shapes and a uniform coating thickness is required.
Brass plating has numerous advantages. The metal is protected from corrosion by the brass coating. Brass protects the surface from moisture, acids and other harmful substances.
The surface of the metal is enhanced by brass plating. The warm golden color of brass is not only aesthetically pleasing, but also gives the metal a high-quality appearance. It is therefore often used for jewelry, fittings, decorative objects and other items where an attractive appearance is important.
In addition, brass plating has the potential to increase the electrical conductivity of the metal. Plating with brass can increase the conductivity of a metal, which can be beneficial in certain situations as brass is a good conductor of electricity.
Copper plating screws and fasteners involves applying a thin layer of copper to the metal surface. Copper plating is often used to protect the metal from corrosion, to create an aesthetic surface or to increase electrical conductivity.
There are various techniques that can be used for copper plating. Electrolytic copper plating is one possible method. In this method, the metal to be used for copper plating is immersed in an electrolyte bath as a cathode. A copper anode is also immersed in the bath. Copper ions are dissolved from the anode by the electric current flow and deposited on the surface of the metal. This forms an even layer of copper on the metal.
An alternative method is chemical copper plating. Here, the metal is immersed in a solution containing copper compounds. Chemical reactions deposit copper ions from the solution onto the surface of the metal. This method is often used when the metal has a complex shape or when a uniform layer thickness is required.
Copper plating offers various advantages. The screws or other fasteners are protected from corrosion by the copper coating. Copper forms a protective layer on the surface that protects the underlying metal from moisture, acids and other harmful influences.
Copper plating also gives the metal a decorative surface. Copper has a warm, reddish color that is aesthetically pleasing and gives the metal a high-quality appearance. Copper plating is often used for jewelry, fittings, decorative objects and other products where an attractive appearance is important.
In addition, copper plating can help to make the metal more electrically conductive. Copper plating can be beneficial in certain situations as it is an excellent electrical conductor.
Silver-plating screws describes the application of a layer of silver to the surface of the screws. This may be done for aesthetic reasons to give the screws a silver appearance or to improve their corrosion resistance.
When silver-plating screws, there are various methods of applying a silver layer. One common method is electrolytic silver plating. The screws are immersed in a silver solution as a cathode and connected to a direct current source. The electrical current flow causes the silver to be deposited from the solution onto the surface of the screws.
Another method is chemical silver plating. Here, the screws are immersed in a solution containing silver ions. A chemical reaction transfers the silver from the solution to the surface of the screws.
Silver plating screws can have various advantages. Firstly, it gives the screws an aesthetically pleasing silver appearance, which may be desirable in certain applications. Secondly, the silver coating can improve the corrosion resistance of the screws, as silver is a noble metal and is less susceptible to corrosion than other metals.
Metal tinning is a process in which a layer of tin is applied to the surface of a metal. This can be done for various reasons, such as to protect against corrosion, to improve solderability or for aesthetic reasons. The tinning process usually involves several steps:
1. pre-treatment: before the metal can be tinned, it must be thoroughly cleaned to remove any impurities, oxidation layers or grease films. This can be done by various methods such as chemical cleaning, mechanical cleaning or pickling.
2. flux: After cleaning, a flux is applied to the surface of the metal. The flux helps to prevent oxidation during the tinning process and allows better wetting of the metal with the tin. There are different types of flux, which are selected depending on the application and type of metal.
3. tinning: After the flux has been applied, the metal is immersed in a tin bath or coated with a tin solution. The tin bath consists of molten tin or a tin alloy. When the metal is immersed, a layer of tin forms on the surface by diffusion or electrolytic deposition.
4. post-tinning: After tinning, post-treatment may be required to remove excess tin or to smooth the tin layer. This can be done by grinding, polishing or other mechanical or chemical processes.
The process of tin plating can vary depending on the type of metal, size and shape of the workpiece. It usually requires specialized equipment and expertise to achieve a high-quality result. Tin plating is used in various industries, such as the electronics industry, in the manufacture of food containers or in the restoration of historical metal objects.
Anodizing screws is a process for the surface treatment of metals, particularly aluminium. It is an electrochemical process in which the screws are treated in an electrolyte solution.
The main reason for anodizing screws is to improve corrosion resistance. The anodizing process forms a thin, hard and protective oxide layer on the surface of the screws. This layer prevents the penetration of moisture and other harmful substances that could cause corrosion. This extends the service life of the screws and maintains their functionality.
In addition, anodizing also offers aesthetic benefits. The oxide layer can be dyed in different colors, giving the screws an attractive appearance. This is particularly important in areas where the screws are visible, such as furniture, vehicles or other decorative applications.
Another reason for anodizing screws is to improve wear resistance. The oxide layer is harder than the underlying metal and therefore offers additional protection against wear and scratches.
Basically, it can be said that the anodizing of screws is carried out for two main reasons: to protect against corrosion and to improve the aesthetic properties. It is a widely used process in many industries to improve the durability and appearance of screws.
The surface treatment of metals, especially steel, is carried out by hot-dip galvanizing connecting parts. It is a process in which the connecting parts are immersed in liquid zinc to create a protective zinc layer on their surface.
The main purpose of hot-dip galvanizing fasteners is to protect them from corrosion. By immersing them in liquid zinc, a layer of zinc is formed on the surface of the connecting parts, which keeps out moisture and other harmful substances. Especially in environments with high humidity or aggressive chemical conditions, this zinc layer provides excellent corrosion protection and significantly extends the service life of the connecting parts.
Hot-dip galvanizing also provides mechanical protection. The connecting parts are protected from scratches, abrasion and other mechanical stresses by the relatively hard and resistant zinc coating. This is particularly important for connecting parts that are exposed to high loads, such as those used in construction, industry or infrastructure.
Hot-dip galvanizing also has the advantage that it is easy to apply. As several connecting parts can be galvanized at the same time, the process is comparatively inexpensive and effective. In addition, the uniform and seamless zinc coating provides a reliable protective layer.
Hot-dip galvanizing of connecting parts is mainly used to protect against corrosion and for mechanical protection. It is a proven process that is used in many areas to improve the durability and reliability of connecting parts, especially in outdoor applications or in aggressive environments.
- Acronym: tZn
- Applicable for threaded parts from M8
- Threadability can be ensured by suitable measures
The coating of a metal with a zinc layer is referred to as inorganic zinc coating. It is an electrochemical process in which metal is immersed in a zinc solution.
Protection against corrosion is the main objective of inorganic zinc coating. The metal is protected from moisture, oxygen and other corrosive substances by the zinc coating. Zinc is an anti-corrosive that sacrifices itself on contact with moisture or oxygen to protect the underlying metal. This process is known as cathodic protection.
The high adhesive strength of the inorganic zinc coating is another advantage. The zinc layer adheres firmly to the metal surface and forms a uniform, gapless coating. This ensures high resistance to abrasion, scratches and mechanical loads.
The inorganic zinc coating also provides high heat resistance. Due to the low melting point, the coating remains stable at high temperatures. This is particularly important for applications where the metal is exposed to high temperatures, such as in the automotive or chemical industries.
Another reason for using inorganic zinc coating is its ease of application. The process is relatively inexpensive and efficient, as several metal parts can be coated at the same time. In addition, the zinc layer is thin and has no effect on the dimensions or weight of the metal.
- Temperature resistant up to approx. 300 °C
- Applicable for threads ≥ M4
Mechanical galvanizing of metal fasteners is a process in which a zinc coating is applied to the surface of bolts and nuts. In comparison to conventional hot-dip galvanizing or inorganic zinc coating, mechanical galvanizing is a process that is carried out without the use of electrolytes or chemical solutions.
With mechanical galvanizing, the screws and nuts are placed in a drum or container filled with zinc powder and special additives, such as glass beads. By rotating or shaking the drum, the nuts and bolts are brought into contact with the zinc powder. The mechanical friction between the fasteners and the zinc powder causes the zinc to be applied to the surface of the nuts and bolts.
The main purpose of mechanical galvanizing of nuts and bolts is corrosion protection. The applied zinc layer forms a protective barrier between the metal of the fasteners and the environment, preventing corrosion. The zinc layer acts as a sacrificial corrosion protection that sacrifices itself on contact with moisture or oxygen to protect the underlying metal.
Mechanical galvanizing also has the advantage of evenly distributing the zinc coating on the nuts and bolts. By shaking or turning in the drum, the zinc powder is evenly applied to the surface of the fasteners, resulting in a seamless coating.
Mechanical galvanizing of fastening solutions also offers the advantage that it has no effect on the dimensions or weight of the fasteners. The applied zinc layer is thin and has no effect on the functionality of the fasteners.
In the chemical blackening process for stainless steel, the surface of the material is blackened by chemical reactions. It is a controlled process in which the outer layer of the stainless steel is transformed into a thin, black oxide layer.
The formation of the black oxide layer gives the stainless steel a dark, matt or shiny surface, giving it an elegant and attractive appearance. This can be particularly important in decorative applications or in the manufacture of jewelry, watches, fittings and other products.
In addition, chemical blackening also offers some practical advantages. The black oxide layer improves the stainless steel's resistance to corrosion and wear. It forms a protective barrier against moisture, oxygen and other harmful substances that could attack the material. The oxide layer can also reduce the reflection of light and thus minimize glare.
Stainless steel chemical blackening involves the use of special chemical solutions or baths that trigger the desired reactions on the surface of the material. The exact composition of the solutions can vary depending on the specific requirements and the desired appearance. The stainless steel is immersed in the chemical bath or the solution is applied to the surface to initiate the reaction and form the black oxide layer.
It is important to note that chemical blackening of stainless steel does not significantly change the properties of the material. The mechanical and chemical properties of the stainless steel remain essentially unchanged, as the oxide layer only forms a thin layer on the surface.
Surface treatment by chemical blackening mainly serves to improve the aesthetic appearance of the stainless steel and also provides a certain degree of corrosion protection.
Burnishing is a process for the chemical surface treatment of metals in which a thin layer of iron oxide is created on the metal surface. This layer gives the metal a dark, black-blue color and also provides a certain degree of corrosion protection.
The burnishing process consists of several steps:
1. cleaning: The metal surface is thoroughly cleaned to remove dirt, grease and other contaminants. This can be done by chemical cleaning, degreasing or mechanical cleaning.
2. activation: The metal surface is activated to facilitate the formation of the black oxide layer. This can be done by applying an activator or by acid pre-treatment.
3. burnishing solution: The metal surface is immersed in a burnishing solution or sprayed with the solution. The burnishing solution usually contains salts such as sodium nitrite or potassium nitrate, which react with the metal surface and enable the formation of the iron oxide layer.
4. reaction: The burnishing solution reacts with the metal surface and forms a thin layer of iron oxide. The reaction time can vary depending on the desired layer thickness and color.
5. neutralization and rinsing: After the reaction, the metal surface is neutralized to stop the chemical reaction. The surface is then thoroughly rinsed with water to remove excess burnishing solution.
6. preservation: To protect the black oxidation layer and improve corrosion protection, a preservation layer can be applied. This can be done by applying oil or wax, for example.
Phosphating is a process for treating the surface of metals in which a phosphate layer is formed on the surface of the workpiece. This is done by immersing the metal in a phosphate solution or applying a phosphate paste.
Phosphating screws is often used to achieve various benefits:
1. improving adhesion: the phosphate layer improves the adhesion of coatings such as varnish, paint or powder coating to the screw surface. This leads to better wear and tear resistance.
2. friction reduction: The phosphate layer can reduce the friction between the screw and the fastened material. This makes it easier to screw in the screw and reduces the risk of damage or deformation of the screw by the fastening material.
3. improved visibility: The phosphate layer can reduce the friction between the screw and the fastened material. This makes it easier to screw in the screw and reduces the risk of damage or deformation of the screw by the fastening material.
4. corrosion protection: The phosphate layer forms a protective barrier on the screw surface to protect it from corrosion caused by moisture, oxygen and other corrosive environments. Subsequent oiling of the screws and fasteners increases the corrosion protection.
Overall, phosphating helps to improve the durability, performance and aesthetics of screws, making them suitable for a wide range of applications.
The treatment of fasteners and screws with a dewatering fluid containing wax is a process aimed at protecting the relevant parts from corrosion and increasing their service life.
Dewatering fluids are special solutions that serve to remove water from the surface of the elements. This is of great importance as water is one of the main causes of corrosion. By removing the water, the risk of corrosion is significantly reduced.
The wax additive in the dewatering fluid fulfills several tasks. The wax forms a protective layer on the surface of the elements, protecting them from moisture and other harmful environmental influences. It improves the frictional properties of the connecting parts, which increases their performance.
The impregnation process with a dewatering fluid containing wax can be carried out as follows:
1. The elements are immersed in the dewatering fluid.
2. The fluid penetrates all surfaces and crevices of the elements and displaces the water.
3. The connecting parts are removed from the fluid and the excess fluid is drained off.
4. The parts are heated to dry the fluid and melt the wax.
5. The melted wax is spread evenly over the surface of the components and forms a protective barrier.
6. After cooling, the fasteners are impregnated and ready for use.
This process is carried out in a controlled environment to ensure that the elements are impregnated evenly and that the impregnation has the desired properties.
Annealing is a heat treatment process used to improve the hardness and strength of steel. For steel fasteners that have been electroplated, annealing is an important step in improving the mechanical properties of the steel and increasing the corrosion resistance of the electroplated coating.
Electroplating is a process in which a thin layer of one metal is applied to the surface of another metal to improve its corrosion resistance, appearance or other properties. For steel fasteners, zinc or nickel electroplating is often used to increase the corrosion resistance of the steel.
After electroplating, the fasteners are annealed to improve their mechanical properties. Annealing is carried out by heating the steel to a certain temperature and then slowly cooling it down. This process changes the microscopic structure of the steel and leads to an improvement in its hardness and strength.
In addition, annealing can help to increase the corrosion resistance of the electroplated coating. By heating and then cooling, the coating can be bonded more firmly to the steel, making it less susceptible to flaking or damage.
Annealing must be carried out carefully to ensure that the desired improvements are achieved without damaging the galvanic coating. This requires precise control of the temperature and cooling rate during the annealing process.
Tribotechnical coatings are specially developed coatings that aim to optimize the tribological properties, i.e. the friction and wear behaviour, of surfaces. They are often used on machine parts that are exposed to high loads or friction, such as gears, bearings, pistons or screws.
The coatings can be made from a variety of materials, including metals, ceramics, polymers or a combination of these materials. They may also contain additives specifically designed to reduce friction or minimize wear.
Tribotechnical coatings can be applied in a variety of ways, including spraying, dipping, electroplating or physical or chemical vapor deposition. The exact process depends on the type of coating and the specific requirements of the application.
The benefits of tribotechnical coatings are numerous. They can help extend the life of machine parts, increase their performance, reduce maintenance requirements and improve energy efficiency. In addition, they can help reduce the environmental impact of machinery and equipment by reducing energy consumption and minimizing the need for lubricants.
" Waxing" is a special coating that is applied to thread-rolling screws. This coating forms a "sliding layer".
The sliding layer has the property of reducing the friction between the screw and the material into which it is screwed. This leads to a reduction in the insertion torque, i.e. the force required to screw the screw into the material.
This process is particularly useful with thread-forming screws, as these screws tend to have a higher insertion torque due to their design. They form their own thread as they are threaded into the material, which creates additional friction. By applying a lubricating layer, this additional friction can be reduced and the screwing in of the screw made easier.
In addition to reducing the insertion torque, the sliding layer can also help to minimize wear on the screw and extend its service life. The effectiveness of the anti-friction coating depends on various factors, including the type of coating, the type of material into which the screw is threaded and the specific application of the screw.
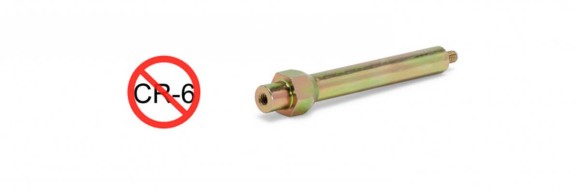
Ban on coatings containing chromium (VI)
Since September 21, 2017, chemicals containing chromium(VI) may no longer be used or placed on the market. In order to keep open the possibility of continued use under the REACH regulation, applications for authorization had to be submitted by March 21, 2016. Since very elaborate proofs or studies are required to obtain authorization, it can be assumed that the number of electroplating companies that will still be offering chromium(VI)-containing coatings (e.g. "yellow galvanized") from 2017 onwards will fall steadily.
The following coatings are affected:
- Galvanized with yellow chromate (e.g. A2C)
- Galvanized with olive chromate coating
- Galvanized with black chromate coating
- Zinc flake coating containing chromium-6 (e.g. Dacromet®)
For this reason, we would like to present you with suitable alternatives (chrome-6 free!):
System | Chromium (IV)-free | White rust (h) | Red rust (h) | Standard | Remark | |||
Coating | Post-treatment | 5 µm | 8 µm | 12 µm | ||||
Zinc (Zn) | Blue chrome-plated | ✓ | 12 | 36 | 72 | 96 | EN ISO 4042 | e.g. A2K, A3K |
Zinc (Zn) | Yellow chrome-plated | X | 48 | 72 | 120 | 144 | EN ISO 4042 | e.g. A2L, A3L |
Zinc (Zn) | Olive chrome-plated | X | 72 | 96 | 144 | 168 | EN ISO 4042 | e.g. A2D |
Zinc (Zn) | Black chrome-plated | X | 12 | - | 72 | 96 | EN ISO 4042 | e.g. A2R |
Zinc (Zn) | Transparent passivated | ✓ | 8 | 48 | 72 | 96 | DIN 50979 | “Thin layer passivation” |
Zinc (Zn) | Iridescent passivated | ✓ | 72 | 144 | 216 | 288 | DIN 50979 | “Thick layer passivation” |
Zinc (Zn) | Iridescent passivated + sealed | ✓ | 120 | 192 | 264 | 360 | DIN 50979 | |
ZincIron (ZnFe) | Iridescent passivated | ✓ | 96 | 168 | 240 | 312 | DIN 50979 | |
ZincIron (ZnFe) | Iridescent passivated + sealed | ✓ | 144 | 216 | 288 | 384 | DIN 50979 | |
ZincIron (ZnFe) | Black passivated + sealed | ✓ | 120 | 192 | 264 | 360 | DIN 50979 | |
ZincNickel (ZnNi) | Iridescent passivated | ✓ | 120 | 480 | 720 | 720 | DIN 50979 | |
ZincNickel (ZnNi) | Iridescent passivated + sealed | ✓ | 168 | 600 | 720 | 720 | DIN 50979 | |
ZincNickel (ZnNi) | Black passivated + sealed | ✓ | 168 | 480 | 720 | 720 | DIN 50979 | |
Zinc flake | Dacromet 320 ® | X | 250 | 600 | 1.000 | - | ISO 10683 | |
Zinc flake | Geomet 321 ® | ✓ | 250 | 600 | 1.000 | - | ISO 10683 | |
Note: If the component hardness exceeds 320 HV or the tensile strength Rm exceeds 1,000 MPa, the manufacturing process must be checked using a test to detect hydrogen embrittlement. In this case, galvanic coating should generally be avoided altogether in order to rule out the risk of hydrogen embrittlement fracture. A zinc flake coating can be an alternative in these cases. All information without guarantee. |
Sonderschrauben Güldner GmbH & Co. KG collects and processes the personal data entered in the form in order to process the requested inquiry for you. Please note the marking of the mandatory fields on the forms. The legal basis for this processing of mandatory data is Art. 6 para. 1 lit. b GDPR, implementation of a pre-contractual measure. The processing of the data voluntarily provided by you is carried out on the basis of Art. 6 para. 1 lit. f GDPR. This permits processing that is necessary to safeguard our legitimate interests. Our legitimate interest is to have contact with you, our customers, to improve the quality of our advice and to be able to contact you more easily in the event of any queries. The data collected will only be stored by us for as long as is necessary to process your request and to contact you. It will then be deleted. Translated with DeepL.com (free version)
Additional data protection information, in particular on your rights to information, rectification, erasure, restriction of processing, objection and complaint, can be found in our privacy policy.